The Comprehensive Guide to Injection Molding of Plastics
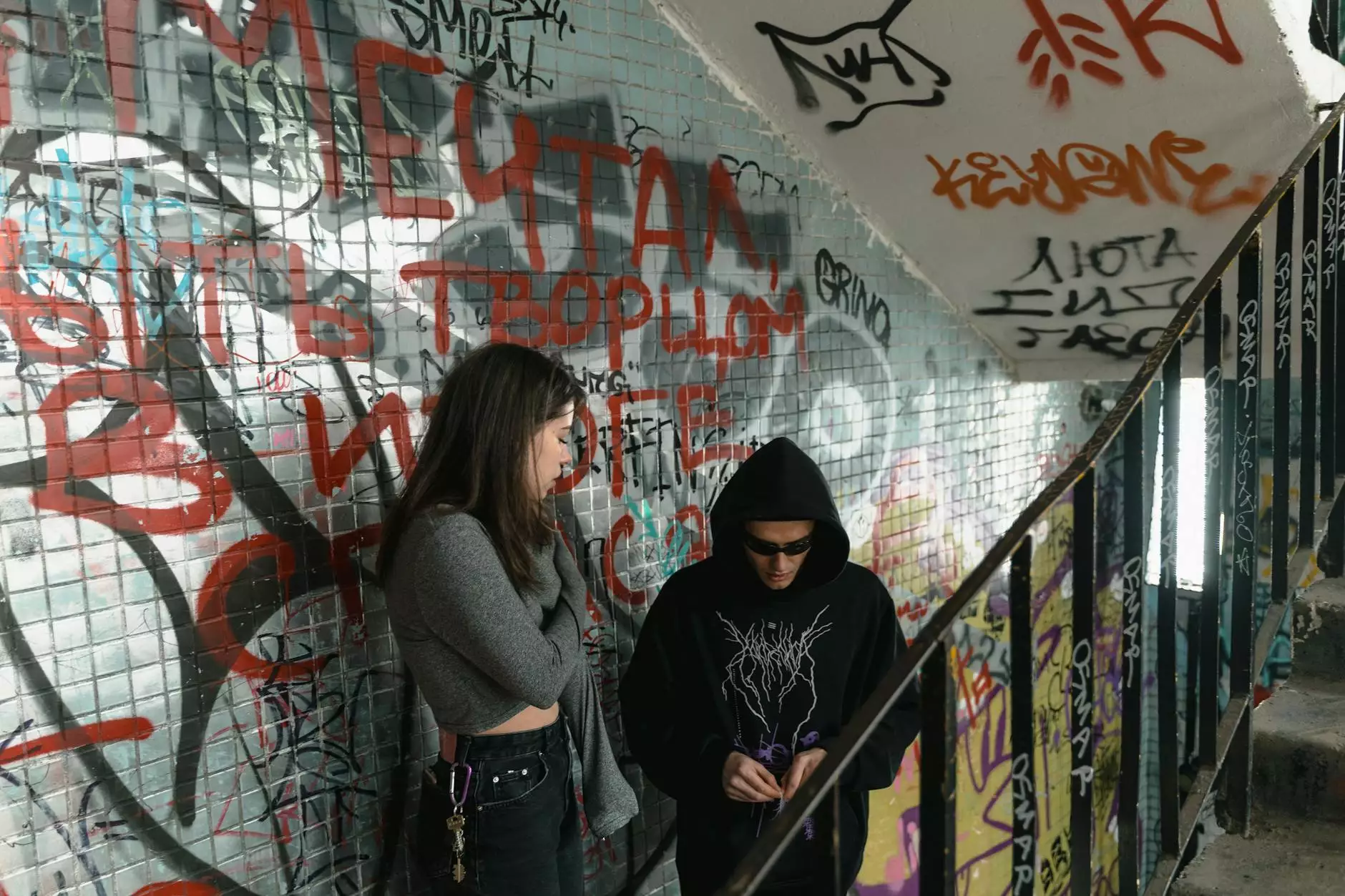
Injection molding of plastics is a pivotal process in the manufacturing industry, enabling the mass production of intricate and precise plastic parts. Through this article, we will delve deep into the processes, advantages, applications, and the essential role of metal fabricators in this field. It is crucial to understand how this technology operates and its significance in modern manufacturing to leverage its benefits effectively.
Understanding Injection Molding
Injection molding is a manufacturing technique that involves the injection of molten plastic material into a custom-designed mold. Once the plastic cools and solidifies within the mold, it takes on the shape of the mold cavity, producing the desired part. This method is celebrated for its ability to create complex shapes with high precision and efficiency.
Processes Involved in Injection Molding
The process of injection molding of plastics consists of several steps, each critical to ensuring the final product meets quality standards.
- Material Selection: The first step involves selecting the appropriate type of plastic. Common materials include ABS, polystyrene, polyethylene, and nylon, among others.
- Melting Phase: The selected plastic resins are fed into a heated barrel where they are melted until they reach the appropriate viscosity for injection.
- Injection Phase: The molten plastic is injected into the mold under high pressure using a screw or plunger system, which ensures that the material fills the mold completely.
- Cooling Phase: Once the mold is filled, the plastic must cool and solidify. Cooling time varies depending on the type of plastic and the part's thickness.
- Mold Opening and Part Ejection: After cooling, the mold opens, and ejector pins release the finished part, which may require further processing.
- Finishing Operations: Depending on the application, additional steps such as trimming, painting, or assembly may be necessary.
Advantages of Injection Molding
The advantages of injection molding of plastics are numerous and significantly contribute to its popularity among manufacturers:
- High Efficiency: Injection molding is remarkably fast, allowing for the production of large quantities of parts in a short amount of time.
- Precision and Consistency: This process offers high levels of precision, making it ideal for detailed parts that require uniformity across batches.
- Design Flexibility: Complex designs can be easily achieved, enabling innovation in product design.
- Waste Reduction: The process generates minimal waste, as excess material can often be recycled.
- Low Labor Costs: Automation is prevalent in injection molding, which reduces the need for extensive manual labor.
Common Applications of Injection Molding
Injection molding of plastics is used across various industries due to its versatility. Here are some of the most common applications:
Automotive Industry
Plastic components in automobiles are crucial for aesthetics and functionality. Parts such as dashboards, bumpers, and interior panels are frequently produced using injection molding.
Consumer Products
Household items ranging from toys to kitchen utensils are often manufactured via this process. It allows for colorful, sturdy, and lightweight products that cater to consumers' preferences.
Medical Devices
The medical industry relies on precision and cleanliness, making injection molding suitable for manufacturing items like syringes, surgical instruments, and other medical components.
Electronics
Injection molding plays a vital role in producing casings, connectors, and other electronic components that require consistent quality and performance.
The Role of Metal Fabricators in Injection Molding
Metal fabricators are essential to the injection molding process, particularly in the creation of molds. Here’s how they contribute:
- Custom Mold Design: Metal fabricators design and create molds tailored to the specifications of the injection molding project, ensuring exact dimensions and shapes.
- Material Expertise: They have in-depth knowledge of various metals, allowing them to select the best materials for mold production based on the application's demands.
- Durability and Longevity: High-quality molds manufactured by skilled metal fabricators can withstand repeated use, making the injection molding process more cost-effective.
- Repairs and Maintenance: Metal fabricators provide services for mold maintenance and repairs, ensuring the longevity and performance of molds over time.
Factors Influencing the Cost of Injection Molding
Understanding the costs associated with injection molding of plastics is crucial for businesses. Several factors influence these costs:
Material Costs
The type of plastic used significantly affects the overall cost. Different resins have varying prices based on availability, quality, and properties.
Mold Complexity
More complex molds require intricate design and fabrication processes, resulting in higher costs. Simpler molds tend to be less expensive.
Production Volume
Higher production volumes can lead to lower costs per unit due to economies of scale. It is often more cost-effective to produce larger quantities.
Lead Time
Shorter lead times may incur additional costs due to rush orders or expedited shipping for materials.
Future Trends in Injection Molding of Plastics
The future of injection molding of plastics seems promising with several trends emerging:
- Advanced Materials: Innovations in material science are leading to the development of new plastics that offer better performance characteristics.
- Sustainability Initiatives: The industry is increasingly focusing on sustainable practices, including the use of recycled plastics and eco-friendly manufacturing methods.
- Smart Manufacturing: Integration of IoT (Internet of Things) technologies is gaining traction, enabling real-time monitoring and optimization of the injection molding process.
- 3D Printing Integration: As 3D printing technology advances, it may complement traditional injection molding, particularly for rapid prototyping.
Conclusion: Embracing the Future of Injection Molding
Injection molding of plastics is a cornerstone of modern manufacturing, offering the perfect blend of efficiency, precision, and versatility. As industries continue to evolve and demand for innovative products rises, embracing advancements in injection molding processes and sustainable practices is essential. By collaborating with skilled metal fabricators and leveraging technological advancements, businesses can not only meet market demands but also lead in their respective markets.
With a firm understanding of the intricacies, advantages, and future trends of injection molding, companies can position themselves strategically within their industries, ensuring they remain competitive and efficient in a rapidly changing business landscape.